おはようございます!シータケ@食品工場です。
今日は「【設備】設備は壊れる前提で設計しよう(フェールセーフについて)」ということで解説していきます。
フェールセーフとは、英語で書くとFail Safeです。Fail(失敗しても)Safe(安心)という意味ですね。
食品工場に限った話ではないかもしれませんが、工場の設備って本当によく壊れます。永久に壊れない設備なんて存在しません。
たとえ設備が壊れたとしてもお客様に迷惑をかけないことが大切ですよね。
設備が壊れても回収事故のような事態に陥らないようにするための戦略として「フェールセーフ」という考え方があります。
今回は実例を交えて紹介していきたいと思います。
この記事を読み終わったら、工場の設備についてより深く理解ができるようになっていると思います。
フェールセーフとは
設備はいつか必ず壊れることを前提とし、故障時や異常発生時でも、安全側に動作するように設備を設計する戦略(コンセプト)のこと。
たとえばわかりやすい例では、踏切遮断機が故障した場合
⇒重力により自らしゃ断かんが降りてくる(自重降下)機構により踏切通行者の安全を確保します。
(日本信号株式会社(NIPPON SIGNAL CO., LTD.)のサイトより)リンク
つまり、我々がよく目にする踏切遮断機ですが、電力を使用してあの棒(遮断機)を上げ続けている設計で、電車が来たときだけ下げているわけではないんですね。
たとえば踏切遮断機が壊れて通電しなくなったり、停電で電気が流れなくなった場合も、自分の重さで踏切が下がってきて遮断することで、最低限みんなの命は守る、という設計になっているのです。
食品工場でのフェールセーフの例
では、食品工場でのフェールセーフの例について、いくつか紹介していきたいと思います。
もちろん、踏切の遮断機と同じで従業員の人命にかかわるような安全面でのフェールセーフもありますが、製品を通じてお客様に迷惑をかけない、食品安全の目線でのフェールセーフを紹介していきたいと思います。
基本排出される設計にしておく
上記した踏切の例に近いですが、「NGだったら排出する」のではなく、「OKなら通過させる」という設計にしましょう。
たとえば、食品工場では食品安全を担保するために色々な検査機があります。その一例が口に入れた時にケガをするような硬質異物を取り除く金属探知機や軟X線検査機だったりします。
一例として以下の写真のようなアームで排出していた場合で例を挙げると、電源が落ちている状態ではアームが「排出側」になるように設計しておきます。そして検査で「OK」の信号が出たときだけアームを上げて「良品」として次工程に進むように設計するのです。
これが出来てないと検査機の電源が落ちたり、排出のアームが壊れて動かなかったり何か問題があったときに「不良品」なのに製品化されてしまうリスクがあるってことですね。
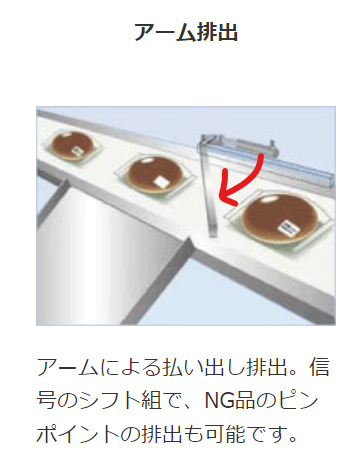
EDM CORPORATION のサイトより リンク
検査機の電源が入ってないとラインが動かせないようにしておく
これも上記に近いですが、食品安全を担保する検査機が稼働していないのにラインが動いてしまう状態は大変危険です。
場合によっては「金属片」や「ガラス片」などが入っているにもかかわらず製品化している可能性も出てきます。(可能性としては低いかもしれませんが)
食品安全を担保するためにいれている検査機の電源入れ忘れや、途中で壊れてしまったようなときにラインが停止するように制御を入れておきましょう。
まとめ
いかがだったでしょうか。このように食品工場でも「フェールセーフ」のコンセプトで製造ラインを設計することが一般的になってきています。
もしどこかの工場を見学するような機会があれば食品安全を担保するためにどんな検査機が入っているか、検査機の後はNG品はどのように排出されるか、排出はフェールセーフになっているか、質問してみてください。
業界の人間だと思われてびっくりされると思いますが、もしかしたら何か教えてくれるかもしれませんね。
今日は以上になります。さよなら!!!
コメント